Unlocking the Secrets of Ultrasonic Transducers: Key Technology in Cleaning, Imaging, and Sensing
Browse Volume:158 Classify:Support
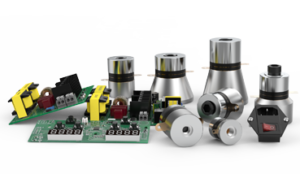
multi-power transducer
In the world of ultrasonic technology, the ultrasonic transducer is a crucial component responsible for converting electrical energy into mechanical vibrations, or vice versa. This simple yet powerful device plays a vital role in a variety of applications, from cleaning and medical imaging to industrial and research purposes. While the overall concept of ultrasonic cleaning and sensing is widely known, the workings of the ultrasonic transducer itself often go underappreciated.
Ultrasonic transducers operate on the principle of piezoelectricity, which enables them to generate high-frequency sound waves that can penetrate surfaces or materials to perform a range of functions. The efficiency and performance of ultrasonic devices heavily depend on the quality of the transducer, making it a core element in any ultrasonic system. This article delves into the types, functions, applications, and maintenance of ultrasonic transducers, providing a comprehensive guide for professionals and enthusiasts alike.
1. Understanding Ultrasonic Transducers
Ultrasonic transducers are devices that convert electrical energy into ultrasonic energy or mechanical vibrations into electrical energy. The most common usage of ultrasonic transducers is in the generation of sound waves in the ultrasonic frequency range, typically between 20 kHz and 40 MHz. These sound waves are then used for a variety of purposes, including cleaning, imaging, welding, and testing materials.
1.1. The Basic Principle of Ultrasonic Transduction
At the core of the ultrasonic transducer lies the principle of piezoelectricity. Piezoelectric materials, such as quartz or lead zirconate titanate (PZT), are capable of producing an electric charge when subjected to mechanical stress. Conversely, they can change shape when an electric field is applied to them. This property is what enables the ultrasonic transducer to produce and receive high-frequency sound waves.
When an alternating current (AC) is applied to the piezoelectric element inside the transducer, it undergoes mechanical deformation, generating vibrations. These vibrations are transmitted through the coupling medium (often water or gel in medical applications), producing ultrasonic sound waves that can be directed toward the target material or surface.
1.2. Types of Ultrasonic Transducers
There are several types of ultrasonic transducers, each designed for specific applications. They vary based on their structure, frequency range, and the materials used in their construction.
- Piezoelectric Transducers: The most common type, these use piezoelectric crystals to generate ultrasonic waves. These transducers are used in both commercial and industrial applications, such as cleaning, diagnostics, and material testing.
- Magnetostrictive Transducers: These transducers use magnetostrictive materials, which change their shape when exposed to a magnetic field. While less common than piezoelectric transducers, they are still used in high-frequency applications like medical imaging.
- Capacitive Transducers: These transducers utilize capacitive plates to generate ultrasonic waves. They are less widely used but have specialized applications in specific fields such as high-resolution imaging.
Each type of ultrasonic transducer has its own strengths, with the choice of transducer typically depending on the application’s specific requirements, such as frequency range, energy output, and precision.
2. The Role of Ultrasonic Transducers in Cleaning Applications
Ultrasonic cleaning is one of the most well-known applications of ultrasonic transducers. Ultrasonic transducers are responsible for generating the high-frequency sound waves that create cavitation bubbles in the cleaning solution. These bubbles implode when they collapse, creating intense microscopic shockwaves that dislodge dirt, oil, and other contaminants from the surface of the items being cleaned.
2.1. The Cleaning Process: Cavitation and Microstreaming
The key to the ultrasonic cleaning process lies in cavitation—the formation and implosion of microscopic bubbles in the cleaning fluid. When ultrasonic waves are generated by the transducer, the pressure fluctuations in the liquid cause small vapor bubbles to form. These bubbles expand and collapse violently, creating high-energy shockwaves that can penetrate microscopic cracks and crevices in the items being cleaned.
As the bubbles collapse, the energy released creates intense shear forces that break apart contaminants, making ultrasonic cleaning highly effective. This process works even for delicate objects, such as jewelry or electronic components, as it avoids the need for abrasive methods that could cause damage.
2.2. Applications of Ultrasonic Cleaning
- Medical Equipment: Ultrasonic cleaning is widely used to clean medical instruments, ensuring that even the smallest contaminants are removed. Surgical instruments, dental tools, and laboratory glassware all benefit from this gentle yet effective cleaning method.
- Electronics: For electronics manufacturers, ultrasonic cleaning is essential for removing flux residues, oils, and other contaminants from circuit boards and sensitive electronic components without causing damage.
- Jewelry: Ultrasonic cleaners are frequently used in jewelry shops to remove dirt, oils, and grime from delicate rings, necklaces, and watches. The precision of the transducer ensures a thorough clean without harming the jewelry.
3. Medical and Diagnostic Uses of Ultrasonic Transducers
Ultrasonic transducers play an integral role in the medical field, especially in diagnostic imaging. Devices like ultrasound machines, which are used for a wide range of applications, rely heavily on transducers to generate and receive ultrasonic waves that allow healthcare professionals to visualize internal structures of the body.
3.1. Ultrasound Imaging
In ultrasound imaging, the transducer both emits and receives ultrasonic waves. When placed on the surface of the skin, it sends high-frequency sound waves into the body. These sound waves bounce off internal structures (like organs, muscles, or tissues) and return to the transducer, where they are converted back into electrical signals. These signals are then processed to create real-time images of the body’s internal structures.
- Pregnancy Scans: One of the most well-known uses of ultrasound transducers is in prenatal care, where they are used to visualize the fetus and monitor its growth and development.
- Cardiovascular Imaging: In cardiology, ultrasonic transducers are used in echocardiograms to assess the heart’s structure and function, helping diagnose conditions such as valve problems or heart failure.
3.2. Non-Destructive Testing (NDT)
Another key application of ultrasonic transducers in medicine and engineering is non-destructive testing (NDT). Ultrasonic testing is used to detect cracks, voids, or other structural problems in materials like metals, plastics, and composites without causing any damage to the object being tested. In the medical field, NDT using ultrasonic transducers is crucial in assessing the condition of implants and prosthetics.
4. Industrial Applications of Ultrasonic Transducers
Ultrasonic transducers are essential in many industrial processes, where they help perform tasks ranging from welding and cutting to cleaning and material testing.
4.1. Ultrasonic Welding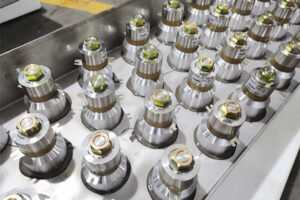
In ultrasonic welding, transducers are used to generate high-frequency vibrations that are transferred to the materials being joined. These vibrations create localized heat, which softens the materials, allowing them to fuse together. Ultrasonic welding is commonly used in industries like automotive manufacturing, electronics, and packaging.
- Automotive Industry: Ultrasonic transducers are used to weld plastic parts in the automotive industry, such as dashboards and interior panels. The precision of ultrasonic welding ensures strong, clean welds without the need for additional fasteners or adhesives.
- Electronics: Ultrasonic transducers are also used for micro-welding in the electronics industry, particularly for joining delicate wires or components that cannot be exposed to high temperatures.
4.2. Ultrasonic Cleaning in Industrial Manufacturing
Beyond their medical and consumer applications, ultrasonic transducers are frequently used in industrial cleaning operations. Ultrasonic cleaning systems are employed to remove contaminants from large industrial components like engine parts, turbines, and molds. The high efficiency of ultrasonic cleaning reduces downtime and improves the overall quality of the manufacturing process.
4.3. Material Testing
Ultrasonic transducers are widely used in material testing, particularly in the aerospace and construction industries, where the integrity of materials must be closely monitored. The ability to detect internal flaws such as cracks or voids within materials makes ultrasonic transducers invaluable in quality control and preventative maintenance.
5. Maintenance and Care of Ultrasonic Transducers
Proper maintenance of ultrasonic transducers is essential for ensuring their longevity and effectiveness. Over time, the transducer can experience wear or damage that can affect its performance, leading to reduced cleaning power or faulty imaging.
5.1. Cleaning and Calibration
- Cleaning: Regular cleaning of the transducer’s surface is essential, especially in applications like medical imaging or industrial cleaning, where contaminants can accumulate. Special care should be taken to avoid using harsh chemicals or abrasive materials that could damage the transducer’s surface.
- Calibration: For medical imaging or industrial testing, ultrasonic transducers should be periodically calibrated to ensure accuracy. Misalignment or wear can cause inaccurate readings, which could result in faulty diagnostics or product defects.
5.2. Replacement of Components
Over time, certain components of the transducer, such as the piezoelectric elements, may degrade or lose efficiency. These elements may need to be replaced to maintain optimal performance. Regular inspection and testing will help detect early signs of wear and ensure that the transducer continues to operate at peak efficiency.
Final Thoughts
The ultrasonic transducer is a critical piece of technology that enables a wide range of applications, from cleaning and welding to medical imaging and material testing. Understanding its design, operation, and maintenance can help ensure that ultrasonic systems perform efficiently and reliably. With the continuous advancements in ultrasonic technology, these devices will only become more versatile, opening up new possibilities for industries and professionals around the world.